Capability Highlight
Nondestructive Inspection
Providing services in a variety of fields to include General Aviation (FAA), DoD Aviation, Ground Equipment, Manufacturing, Powerplants and many others.
HIGHLY ACCURATE INSPECTION TECHNIQUES
Backed by our combined inspection time of 70,000 hours, our extensive knowledge will guarantee every inspection is completed with the highest degree of accuracy possible. We have experience in a variety of inspection techniques to include immersion and contact UT, phased array UT, surface and subsurface ET, film radiography, Methods A,C and D Penetrant systems, and MT inspections utilizing AC/ DC current on portable and stationary inspection systems.
CERTIFICATIONS
Over 80 years in combined Nondestructive Testing (NDT) experience NAS410 Certified Level II in Penetrant Testing (PT), Magnetic Particle Testing (MT), Ultrasonic Testing (UT), and Eddy Current Testing (ET).
SKILLED TEAM EXPERIENCE:
- NAS410 Level III
- SNT-TC-1A
- T9074-AS-GIB-010/271
- ASME Section V Article 1 Level III certified in Penetrant Testing (PT)
- Magnetic Particle Testing (MT)
- Visual Testing (VT)
- Radiographic Testing (RT)
- Ultrasonic Testing (UT)
- American Society of Nondestructive Testing (ASNT) Level III in PT, MT, VT, RT, UT
- American Welding Society (AWS)
- Certified Welding Inspector (CWI)
UTILIZING ADVANCED TECHNOLOGIES
Eddy Current
Olympus Nortec 600
This methods allows us to find material defects at very early stages before defects cause catastrophic failures.
- Utilizing several standards of various materials such as aluminum, stainless steel, and titanium, we can detect surface as well as subsurface defects.
- Measure metal thickness, coating thickness (paint), heat treat verification, metal identification, and bolt hole inspections.
- Can be used during manufacturing process or in-service parts.
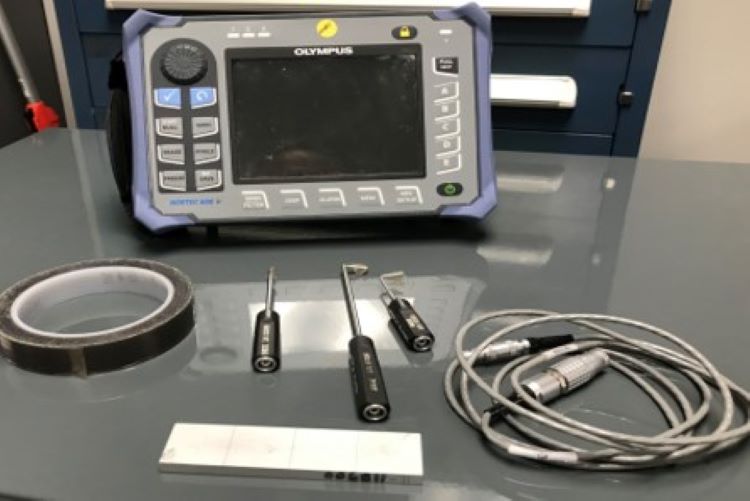
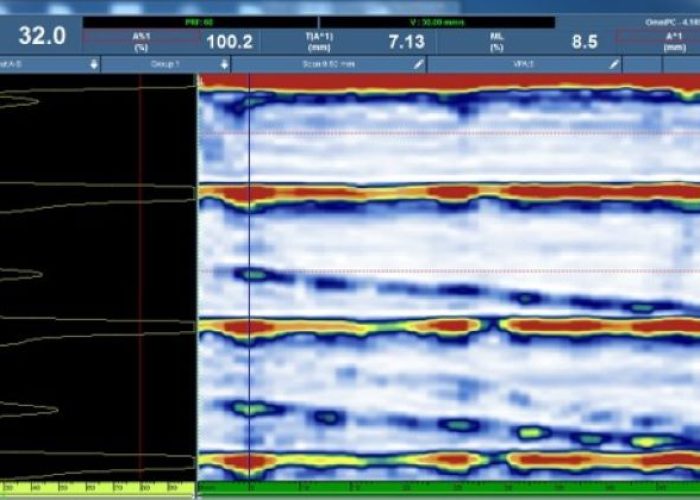
Ultrasonic TESTING
Olympus Epoch 650/ Omniscan SX
These inspection units allow us to perform a wide range of inspections to meet any future needs.
- Inspectable materials include metal, composite, and some rubbers/ plastics
- Thickness Testing
- Defects such as cracks, laps and inclusions
- Equipment available for Phased Array inspections (Omniscan SX and Rollerform)
- Phased Array inspections provide a high degree of detail and allow you to view the inspection area as well as any defects as a 2D or 3D picture.
This methods allows us to find material defects at very early stages before defects cause catastrophic failures and can be used during manufacturing process or in service parts.
BOND TESTING
Olympus Bondmaster 600
Similar process to Ultrasonic Testing except utilizing lower frequencies (sonic sound). Unique equipment that is primarily used to find voids/ disbonds in composite materials such as fiber glass, carbon fiber and honeycomb.
- Capable of finding discontinuities between composite plies or prefabricated parts that are bonded together.
- Able to find disbonds between laminated sheet metal.
- Can be used during the manufacturing process or in-service inspection.
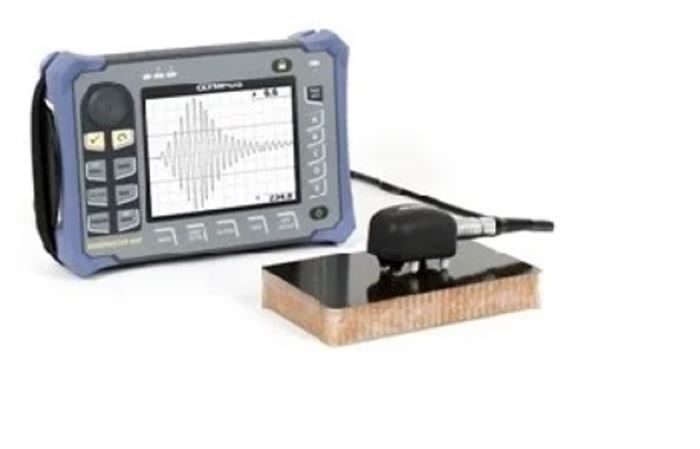
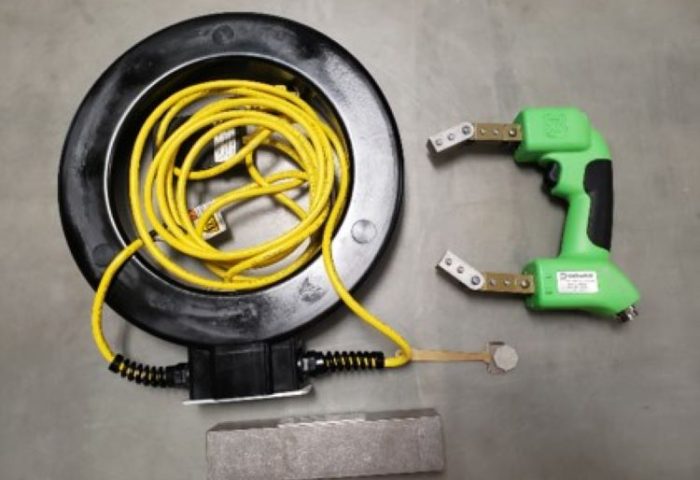
Magnetic Particle
This method uses AC or DC current to induce a magnetic field allowing us to identify surface as well as subsurface defects.
Yoke – This equipment is used to induce localized magnetic fields in large parts that require spot checks
Coil – Used to induce a magnetic field in long parts that can fit within the coil
These tools allow for ease of inspection on large parts without the need for large scale equipment. They can be used on in production and in-service parts and used to inspect ferromagnetic materials.
Fluorescent Penetrant- Method
This technique finds defects open to the surface with the help of capillary action and several other factors. Method C inspections allows us to do spot checks without the need of large scale or expensive equipment.
- Small defects are easily detectable.
- Utilizing a blacklight, inspections are done in a darkened room so cracks can be more easily seen.
- 200:1 probability of crack/ surface defect detection.
- Used for production and in-service parts.
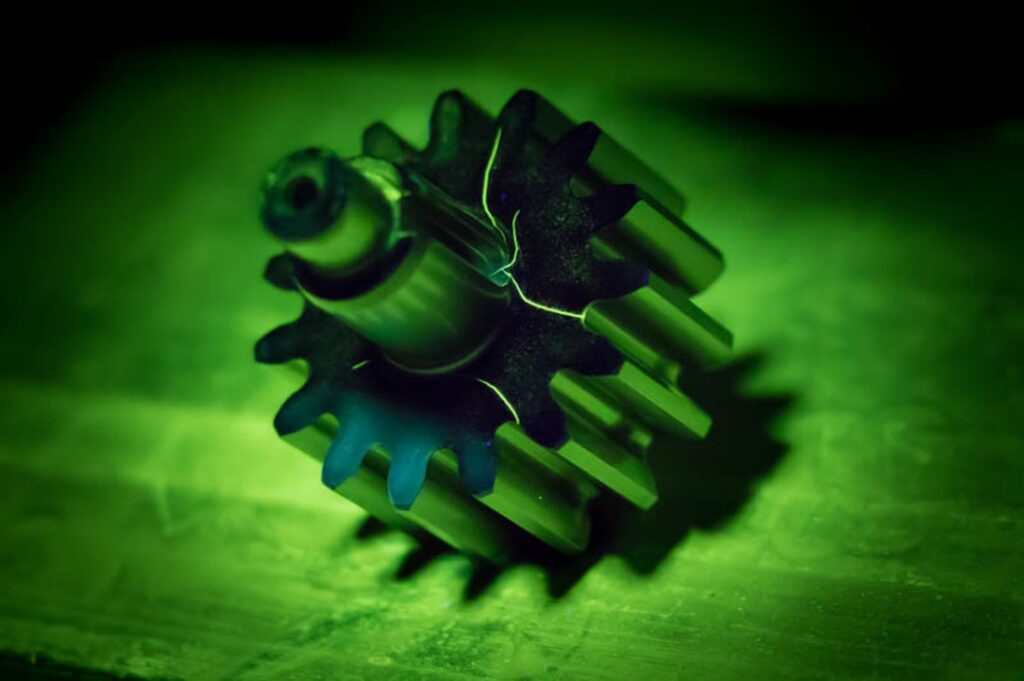